2021年6月17日
国立研究開発法人新エネルギー・産業技術総合開発機構
新構造材料技術研究組合
NEDOが進める「革新的新構造材料等研究開発」において、今般、新構造材料技術研究組合(ISMA)は、新幹線がトンネルを出入りする際に繰り返し荷重のかかる客室一般部を模擬した大型の部分構体(高さ2.9m×幅3.4m×長さ5.0m)を作製し、車両の設計寿命である20年間のトンネル出入り分に相当する14.7万回の気密疲労試験を実施しました。その結果、難燃性マグネシウム合金を使用した部分構体が、長期間の運用に耐えられることを確認しました。
この部分構体は難燃性を向上させたマグネシウム合金で作製しており、軽量なアルミニウムよりさらに比重が30%以上小さいため、車両の大幅な軽量化と高い信頼性を両立することができます。今後、鉄道車両の客室内装材や機器のカバーなどへの難燃性マグネシウム合金の適用事例を増やすことで市場を開拓し、次世代以降の新幹線向けとして全長20~25mの構体への難燃性マグネシウム合金の本格適用を目指します。
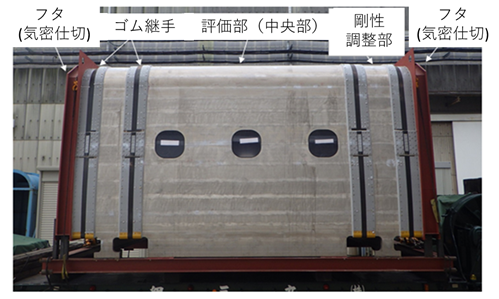
図1 客室一般部を模擬した高速鉄道車両の部分構体(長さ5m)の外観
1.概要
現在、新幹線などの高速鉄道では、車両構体に軽量なアルミニウム合金が使われるのが一般的ですが、鉄道の高速化と省エネ化の重要度が増していることを背景に、近年はさらなる軽量化ニーズが高まっています。アルミニウムよりも比重が30%以上小さいマグネシウムは、軽量化を実現する材料として注目されており、鉄道だけでなく自動車や宇宙・航空分野でもマグネシウム合金を用いた大型構造物の早期実用化が期待されています。
しかし、マグネシウム合金による展伸材※1は難燃性や耐食性、成形性などが比較的低いことから電子筐体(きょうたい)や機械部品などの小型部材への使用が大半で、大型構造物への適用事例はほとんどありませんでした。
こうした中、国立研究開発法人新エネルギー・産業技術総合開発機構(NEDO)は2014年度から「革新的新構造材料等研究開発※2」に取り組んでおり、同事業で新構造材料技術研究組合(ISMA)は、大型構造物である高速車両の構体への適用を目的に、強度や延性、加工難易度を改善した難燃性マグネシウム合金※3を開発しました。2016年には難燃性マグネシウム合金を使った車両の側構体部分のパネル試作、また2018年までには現行の新幹線車両と同一サイズの断面をもつ高速鉄道車両の部分構体(高さ2.9m×幅3.4m×長さ1.0m)の試作に成功し、大型構造物を作製できることを実証しました。そして今般、新幹線のトンネル出入り時の反復荷重に対する疲労強度を確認するため、さらに大型の部分構体(高さ2.9m×幅3.4m×長さ5.0m)を作製し、設計寿命20年間のトンネル出入り分に相当する14.7万回の気密疲労試験※4を実施し、難燃性マグネシウム合金を使用した部分構体が長期間の運用に耐えられることを確認しました。
なお、本研究成果はISMAが2021年7月1日に開催する革新的新構造材料等研究開発「2020年度成果報告会」でオンライン発表する予定です。詳細は、以下成果報告会イベントページをご覧ください。
2.今回の成果と役割分担
(1)気密疲労試験構体の設計
新幹線などの高速車両ではトンネル出入り時の圧力荷重(気密荷重)が高く、通常の鉄道車両で適用されている疲労限度の設計※5が困難なため、気密疲労荷重を基準とした有限の設計寿命(安全寿命設計)が適用されています。今回の構体の設計に際しては、20年間の運用に耐えうる疲労強度の目標として溶接部にアルミニウム合金製と同等の疲労強度を付与することを設定し、「70MPaの繰り返し応力に14.7万回耐えることができる疲労強度」を採用しました。これを実現するため、最大気密荷重7.8kPaが負荷された状態で試験構体の強度が最も弱い溶接部に70MPa以上の応力が作用しない構造設計を行うとともに、70MPaに近い繰返し応力が溶接部に作用しても破壊しない形状を新たに考案しました(図2)。
また、設計した部分構体での客室中央部を模擬した気密疲労試験は、試験構体内部に圧力をかけ応力を発生させるため、輪切り状の構体の両端をフタ(気密仕切)でふさぐ必要があります(図1)。しかし、フタ近くの構体の変形はフタの存在により評価部(中央部)と比較してわずかになるため、従来は全長10m程度の輪切り状の構体を作製し、評価部(中央部)とフタの距離を十分にとって変形を評価していました。これに対し、今回は試験場や輸送の事情で試験構体の全長を5mとする制約もあり、フタと評価部(中央部)の輪切り状の構体の間の結合方法を工夫することで、客室一般部としての評価が行えるようにしました。具体的には、図1に示すように客室一般部を模擬した評価部(全長3m)の外側に剛性※6が高い剛性調整部を設け、その外側に配置したフタをゴム継手で接合する構造を採用することで、長さ5mの試験構体でも客室一般部の疲労強度が評価できるようになりました。
(2)気密疲労試験用構体の作製
気密疲労試験用構体(図1)の屋根部(図3(a))および側面部(図3(b))は、難燃性マグネシウム合金(AX41合金)のダブルスキン形材※7を使用し、床板および横はり部(図3(c))は難燃性マグネシウム合金(AX92合金)の中実形材を使用しました。また、ゴム継手の固定部には難燃性マグネシウム合金(AX81G合金)の圧延板材を適用し、フタには鉄製の部品を使用しました。ダブルスキン形材の溶接部の形状は図2(b)に示す通り、面板厚さ(t)に対する溶接部開先深さ(h)を従来よりも25%~40%程度厚くし、気密疲労試験に耐える形状を採用しました。床板同士の接合には摩擦攪拌接合(FSW)※8を適用し、その他の部分はMIG溶接※9を採用、また評価部、剛性調整部、フタの接続には、前述のゴム継手を採用しました。
作製した試験構体の寸法は高さ2.9m、幅3.4m、長さ5.0mであり、試験構体の評価部(中央部)の単位長さ当たりの構体質量は192kg/mでした。この値は2018年に作製した難燃性マグネシウム合金製の部分試作構体(長さ1m)とほぼ同じであり、質量を増加させることなく必要な疲労強度を確保することができました。
なお、この値は現在の新幹線車両に使われているアルミニウム合金製構体(約300kg/m)と比較して30%強の軽量化となっています。
(3)気密疲労試験の実施
神奈川県横浜市の総合車両製作所を出発した試験構体は、試験場となる兵庫県尼崎市で加圧装置やひずみゲージなどを取り付けた後に(図4 (a)、(b))、所定の荷重が負荷できるかを確認した上で気密疲労試験を実施しました(図4 (c)、(d))。予備試験後からは荷重繰り返し回数を進め、夜間の自動運転を開始することで進捗を早め、2021年1月23日には荷重の繰り返し数が目標の14.7万回に達し、試験を完了しました。
気密疲労試験の期間中、評価部(中央部)の溶接部について浸透探傷試験(PT)※10を4回実施した結果、疲労試験において溶接部および溶接部近傍に新たな亀裂の発生や進展は見つからず、難燃性マグネシウム合金で作製した構体の安全寿命設計の高い信頼性を実証することができました。
(4)試験構体の設計・製作、評価に参加した主な研究機関と役割
3.今後の予定
本事業で難燃性マグネシウム合金の適用による高速鉄道車両用の構体軽量化を実証するとともに、上記2.(4)にある材料開発(素形材・合金)、加工・接合、防食、そして部分構体の作製・評価、により安全寿命設計での疲労強度の評価が実証できたことで、設計技術は実用化の域に達したと考えています。
一方、難燃性マグネシウム合金で作製した構体の実用化には、全長20m~25mの構体作製が不可欠で、大きな設備投資が必要となります。これには、難燃性マグネシウム合金の市場を開拓し、投資が可能となる環境へと熟成させることが重要です。このためNEDOとISMAは、まだ鉄道で使用例のない難燃性マグネシウム合金のニーズを鉄道事業者から掘り起こすことを目的に、鉄道車両の客室の内装材や機器のカバーなどへの適用の実施例を増やしていくことを推進しています。
【注釈】
- ※1 展伸材
- 圧延、押出、鍛造など、塑性加工(材料に大きな力を加えて変形させることによって目的とする形状に加工すること)によって作製した金属材料のことです。
- ※2 革新的新構造材料等研究開発
-
- 事業期間:2014年度~2022年度
- 事業内容:鉄鋼、非鉄(チタン、アルミニウム、マグネシウム)、炭素繊維強化プラスチック(CFRP)といった構造材料の特性を向上させ、自動車や鉄道車両などの輸送機器の軽量化を図る事業です。
- ※3 難燃性マグネシウム合金
- 汎用マグネシウム合金(Mg-Al系合金)にカルシウムなどを数%添加することで発火温度を200℃~300℃上昇させ、大気中での溶解・鋳造を可能とした合金です。NEDO事業では、押出し加工性に優れた難燃性マグネシウム合金としてAX41合金を、強度と延性のバランスに優れた合金としてAX92合金やAX81G合金などを開発しました。
- ※4 気密疲労試験
- 高速で走行する新幹線では、車内に急激な気圧変動により乗客に耳の不快感を与えることがあり、それを防止するために車体は気密構造になっています。このため、車内外に圧力差が発生し、トンネルの出入りの度に、車体の膨張と収縮が起きます。気密疲労試験は、この車体の膨張と収縮の繰り返しを模した試験で、高速車体構造の安全性を確認する試験法の一つです。
- ※5 疲労限度の設計
- 疲労限度とは、材料の疲労において、物体が振幅一定の繰り返し応力を受けるとき、何回負荷を繰り返しても疲労破壊に至らない、またはそのように見なされる応力値のことです。疲労限度の設計とは、構造物の最弱部にかかる応力を疲労限度以下に抑える設計のことです。
- ※6 剛性
- 曲げやねじりの力に対する寸法変化(変形)のしづらさの度合いのことです。所定の力に対して構造体の変形が小さい時は剛性が高いです。
- ※7 形材
- パイプ状や棒状などの所定の形状を付与した押出材。ダブルスキン形材は、トラス状(三角形を基本単位としその集合体で構成する形式)の断面を持つ形材であり、中実形材は中身が詰まった形材です。
- ※8 摩擦攪拌接合(FSW)
- FSWとはFriction Stir Weldingの略で、材料の溶融を伴わない固相接合法の一つで、1991年に英国のTWI(The Welding Institute)で開発された接合技術です。極度の摩擦熱と圧力を加えることで生じる金属の塑性流動現象を利用し、金属材料を接合する技術。高熱で溶かして接合する溶接技術と比べて、溶融部分が盛り上がらず平坦にできる、異なる金属材料を接合できる、強度が維持できるといった利点があります。
- ※9 MIG溶接
- MIGとはMetal Inert Gasの略で、母材と溶加材を電極としてその間にアーク(発光放電)を発生させ、その熱によって溶加材を溶かし落着させるアーク溶接の一つです。アーク溶接法は溶融金属の酸化、窒化を防ぐため使用するシールドガスに不活性ガスのみを使い、金属電極棒が溶加材として送給ローラーで自動的に母材に送り込まれ、そのまま溶融して溶接する方式で、通常半自動溶接として使われます。長い距離の連続溶接が可能でロボットを使用するような自動溶接に適しています。
- ※10 浸透探傷試験(PT)
- PTとはLiquid Penetrant Testingの略で、目視しにくい大きさの傷を見えるようにして行う非破壊検査手法です。はじめに、蛍光色を発する浸透液を試験する表面に塗布します。試験面に開口した傷があると、浸透液は傷の内部に浸透して行きます。次に、現像剤と呼ばれる溶剤を塗布し、毛細管現象により傷の内部に浸透した浸透液を試験面まで吸い出します。これにより、傷の内部に浸透した浸透液が試験体表面に広がり、傷を知覚しやすくする手法です。
4.問い合わせ先
(本ニュースリリースの内容についての問い合わせ先)
NEDO 材料・ナノテクノロジー部 担当:小川、廣井、伊東、笹木 TEL:044-520-5220
ISMA 技術企画部 担当:堀谷 TEL:03-6213-5655
(その他NEDO事業についての一般的な問い合わせ先)
NEDO 広報部 担当:坂本、橋本 TEL:044-520-5151 E-mail:nedo_press@ml.nedo.go.jp
(その他ISMA事業についての一般的な問い合わせ先)
ISMA 技術企画部広報室 担当:兵藤 TEL:03-6213-5655 E-mail:pr@isma.jp
関連ページ
June 17, 2021 at 12:03PM
https://ift.tt/3xxyXAp
高速鉄道車両向け難燃性マグネシウム合金製の部分構体で気密疲労試験を実施 - NEDO 新エネルギー・産業技術総合開発機構
https://ift.tt/2Zi3y55
Mesir News Info
Israel News info
Taiwan News Info
Vietnam News and Info
Japan News and Info Update
Bagikan Berita Ini
0 Response to "高速鉄道車両向け難燃性マグネシウム合金製の部分構体で気密疲労試験を実施 - NEDO 新エネルギー・産業技術総合開発機構"
Post a Comment